Design, modeling, and experimental evaluation of a self-sealing component for rotary shafts in magneto-rheological fluid devices
Author affiliations
DOI:
https://doi.org/10.15625/0866-7136/19024Keywords:
magnetorheological fluid (MRF), MRF seal, optimal design, permanent magnetAbstract
This study focuses on the development and evaluation of a self-sealing component for rotary shafts in Magneto-rheological (MR) fluid-based devices, such as MR brakes and MR clutches. The proposed sealing component, which replaces traditional lip-seals, consists of a permanent magnet and a magnetic core positioned on the rotary shaft. Through a combination of simulation and experimentation, the design and performance of the self-sealing component are investigated. Initially, the research provides an overview of MR fluid and its applications, as well as previous studies on sealing components utilizing MR fluid. Building on this background, a configuration for the self-sealing component specific to rotary shafts in MR fluid-based devices is proposed. The design and modeling of the sealing component are carried out, employing the Bingham plastic rheological model of the MR fluid and finite element analysis techniques. Through finite element analysis, an optimal design for the sealing component is determined. Prototypes of the sealing component are manufactured, and experimental testing is conducted to assess its performance characteristics. The experimental results are then compared with the simulated results, allowing for a comprehensive evaluation of the sealing component's effectiveness.
Downloads
References
W. I. Kordonski and S. R. Gorodkin. Magnetorheological fluid-based seal. Journal of Intelligent Material Systems and Structures, 7, (1996), pp. 569–572.
L. Matuszewski and Z. Szydło. The application of magnetic fluids in sealing nodes designed for operation in difficult conditions and in machines used in sea environment. Polish Maritime Research, 15, (2008), pp. 49–58.
H. Urreta, G. Aguirre, P. Kuzhir, and L. N. L. de Lacalle. Seals based on magnetic fluids for high precision spindles of machine tools. International Journal of Precision Engineering and Manufacturing, 19, (2018), pp. 495–503.
C. Hegger and J. Maas. Smart sealing for magnetorheological fluid actuators. Journal of Intelligent Material Systems and Structures, 30, (2018), pp. 689–700.
M. Kubík, D. Pavlíček, O. Macháček, Z. Strecker, and J. Roupec. A magnetorheological fluid shaft seal with low friction torque. Smart Materials and Structures, 28, (2019).
Q.-H. Nguyen, Y.-M. Han, S.-B. Choi, and N. M.Wereley. Geometry optimization of MR valves constrained in a specific volume using the finite element method. Smart Materials and Structures, 16, (2007), pp. 2242–2252.
M. I. Varela-Jiménez, J. L. V. Luna, J. A. Cortés-Ramírez, and G. Song. Constitutive model for shear yield stress of magnetorheological fluid based on the concept of state transition. Smart Materials and Structures, 24, (2015).
Q. H. Nguyen and S. B. Choi. Optimal design of a novel hybrid MR brake for motorcycles considering axial and radial magnetic flux. Smart Materials and Structures, 21, (2012).
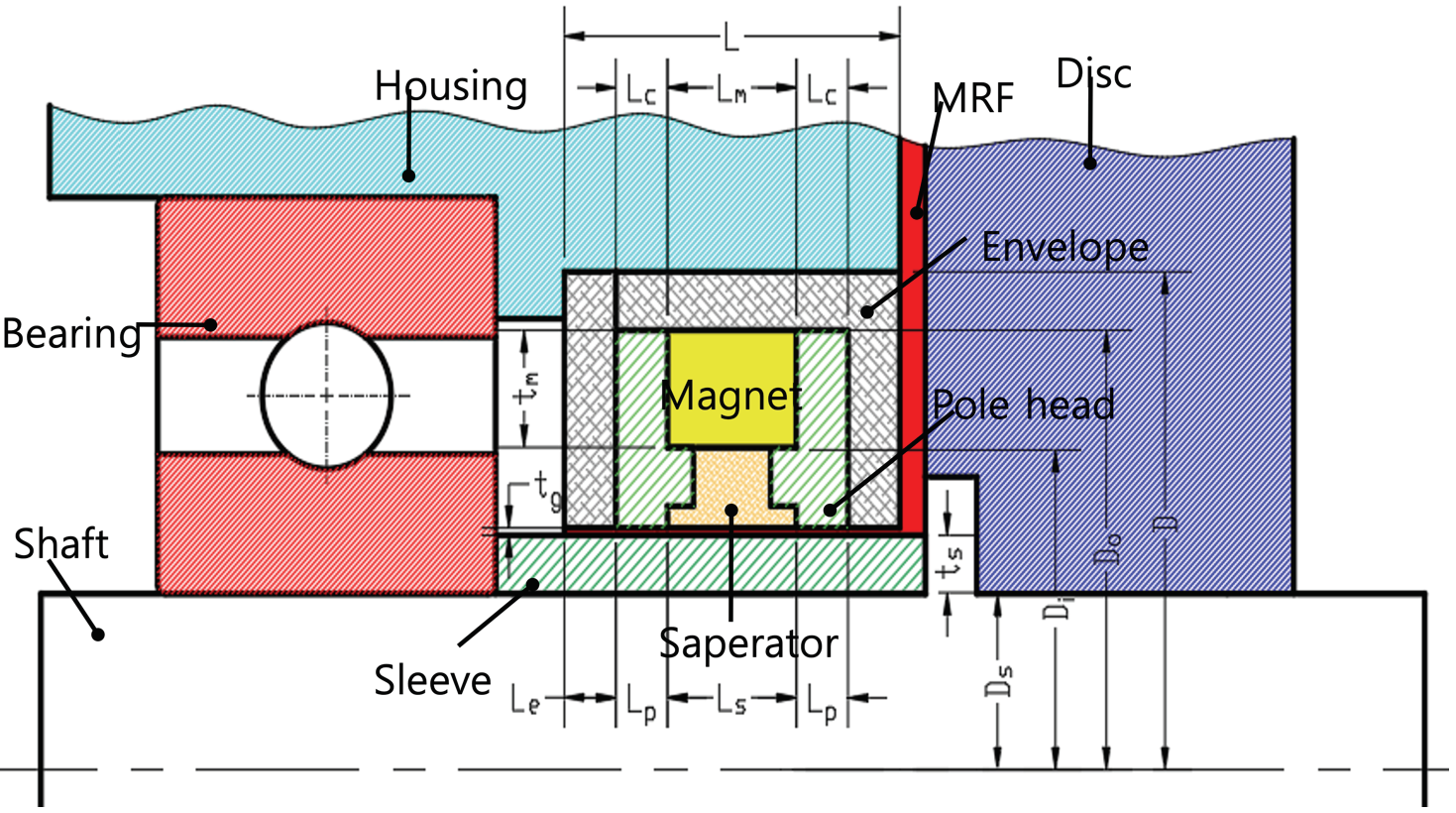
Downloads
Published
How to Cite
License

This work is licensed under a Creative Commons Attribution-ShareAlike 4.0 International License.
Funding data
-
Bộ Giáo dục và Ðào tạo
Grant numbers B2022-VGU-03