Design of a tooth-shaped magnetorheological brake with multiple coils
Author affiliations
DOI:
https://doi.org/10.15625/0866-7136/21128Keywords:
magnetorheological fluid (MRF), magnetorheological brake (MRB), optimal design, ANSYS workbenchAbstract
This research presents an optimized design for a tooth-shaped magnetorheological brake (MRB) with multiple coils. The MRB configuration consists of a disk immersed in magnetorheological fluid (MRF), where four coils act as electromagnets when an electric current is applied. The energized coils induce the alignment of suspended particles in the MRF, forming a chain-like structure that increases the fluid's viscosity. This rapid, strong, and controllable phenomenon enables the MRB to find applications in haptic systems, tension control, and industrial braking systems. To analyze the electromagnetic behavior of the brake, Finite Element Method (FEM) simulations are conducted using ANSYS APDL, and the optimization process is performed utilizing ANSYS Workbench software. The software provides optimized geometries for the brake, resulting in significant improvements in desired performance aspects compared to prior designs, etc.
Downloads
References
[1] Q.-D. Bui, Q. H. Nguyen, and L.-V. Hoang. A control system for MR damper-based suspension of front-loaded washing machines featuring magnetic induction coils and phase-lead compensator. Journal of Intelligent Material Systems and Structures, 34, (2022), pp. 631–641. https://doi.org/10.1177/1045389x221117492.
[2] K. Kluszczyński and Z. Pilch. The choice of the optimal number of discs in an MR clutch from the viewpoint of different criteria and constraints. Energies, 14, (2021). https://doi.org/10.3390/en14216888.
[3] G. Hu, L. Wu, and L. Li. Torque characteristics analysis of a magnetorheological brake with double brake disc. Actuators, 10, (2021), p. 23. https://doi.org/10.3390/act10020023.
[4] N. D. Nguyen, T. Le-Duc, L. D. Hiep, and Q. H. Nguyen. Development of a new magnetorheological fluid–based brake with multiple coils placed on the side housings. Journal of Intelligent Material Systems and Structures, 30, (2018), pp. 734–748. https://doi.org/10.1177/1045389x18818385.
[5] H. Qin, A. Song, X. Zeng, and S. Hu. Design and evaluation of a small-scale multi-drum magnetorheological brake. Journal of Intelligent Material Systems and Structures, 29, (2018), pp. 2607–2618. https://doi.org/10.1177/1045389x18770878.
[6] Q. H. Nguyen and S. B. Choi. Selection of magnetorheological brake types via optimal design considering maximum torque and constrained volume. Smart Materials and Structures, 21, (2011). https://doi.org/10.1088/0964-1726/21/1/015012.
[7] N. Q. Hung and C. S. Bok. Optimal design of a T-shaped drum-type brake for motorcycle utilizing magnetorheological fluid. Mechanics Based Design of Structures and Machines, 40, (2012), pp. 153–162. https://doi.org/10.1080/15397734.2011.616479.
[8] Q. H. Nguyen, V. B. Nguyen, H. D. Le, D. Q. Duyen, W. Li, and N. X. Hung. Development of a novel magnetorheological brake with zigzag magnetic flux path. Smart Materials and Structures, 30, (2021). https://doi.org/10.1088/1361-665x/ac3430.
[9] Q. H. Nguyen and S. B. Choi. Optimal design of an automotive magnetorheological brake considering geometric dimensions and zero-field friction heat. Smart Materials and Structures, 19, (2010). https://doi.org/10.1088/0964-1726/19/11/115024.
[10] N. V. Quoc, L. D. Tuan, L. D. Hiep, H. N. Quoc, and S. B. Choi. Material characterization of MR fluid on performance of MRF based brake. Frontiers in Materials, 6, (2019). https://doi.org/10.3389/fmats.2019.00125.
[11] N. D. Nguyen, T. T. Nguyen, D. H. Le, and Q. H. Nguyen. Design and investigation of a novel magnetorheological brake with coils directly placed on side housings using a separating thin wall. Journal of Intelligent Material Systems and Structures, 32, (2021), pp. 1565–1579. https://doi.org/10.1177/1045389x21993912.
[12] V. B. Nguyen, H. D. Le, Q. H. Nguyen, D. Q. Duyen, D. H. M. Hieu, and S.-B. Choi. Design and experimental evaluation a novel magneto-rheological brake with tooth shaped rotor. Smart Materials and Structures, 31, (2021). https://doi.org/10.1088/1361-665x/ac38ff.
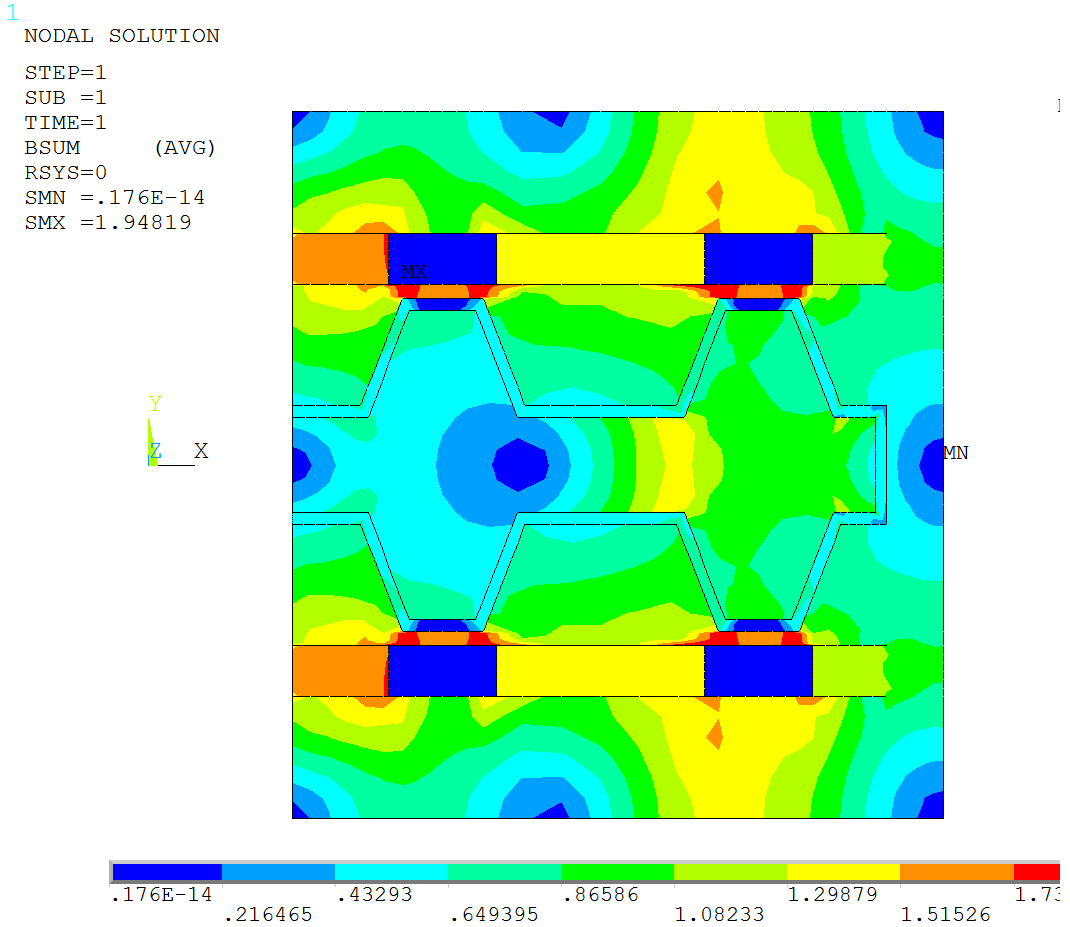
Downloads
Published
How to Cite
License

This work is licensed under a Creative Commons Attribution-ShareAlike 4.0 International License.
Funding data
-
Bộ Giáo dục và Ðào tạo
Grant numbers B2022-VGU-02