Multi-objective optimization of magnetorheological clutch with stationary housing
Author affiliations
DOI:
https://doi.org/10.15625/0866-7136/17979Keywords:
magnetorheological fluid (MRF), magnetorheological clutch, multi-objective optimization, speed controlAbstract
This study focuses on the development of magnetorheological fluid (MRF) based clutch systems for speed control of a rotary load. A new configuration for speed control of a rotary shaft using a magnetorheological clutch (MRC) with stationary winding housing and its mathematical model are proposed based on the Bingham plastic model of MRF. Multi-objective design optimization for MRCs simultaneously considering power consumption, transmitting torque, and rotating mass is then studied based on the derived mathematical model and electromagnetic finite element analysis (FEA) of the MRC. Subsequently, an optimal configuration of the proposed MRC is manufactured and experimentally investigated.
Downloads
References
J. Wang and G. Meng. Magnetorheological fluid devices: Principles, characteristics and applications in mechanical engineering. Proceedings of the Institution of Mechanical Engineers, Part L: Journal of Materials: Design and Applications, 215, (2001), pp. 165–174.
A. Muhammad, X. liang Yao, and Z. chao Deng. Review of magnetorheological (MR) fluids and its applications in vibration control. Journal of Marine Science and Application, 5, (2006), pp. 17–29
U. Lee, D. Kim, N. Hur, and D. Jeon. Design analysis and experimental evaluation of an MR fluid clutch. Journal of Intelligent Material Systems and Structures, 10, (1999), pp. 701–707.
T. Kikuchi, K. Ikeda, K. Otsuki, T. Kakehashi, and J. Furusho. Compact MR fluid clutch device for human-friendly actuator. Journal of Physics: Conference Series, 149, (2009).
D. Wang and Y. Hou. Design and experimental evaluation of a multidisk magnetorheological fluid actuator. Journal of Intelligent Material Systems and Structures, 24, (2012), pp. 640–650.
K. H. Latha, P. U. Sri, and N. Seetharamaiah. Design and manufacturing aspects of magnetorheological fluid (MRF) clutch. Materials Today: Proceedings, 4, (2), (2017), pp. 1525–1534.
Q. H. Nguyen and S.-B. Choi. A new method for speed control of a DC motor using magnetorheological clutch. In W.-H. Liao, editor, SPIE Proceedings, SPIE, (2014).
Q. H. Nguyen and S.-B. Choi. A new method for speed control of a DC motor using magnetorheological clutch. In Active and Passive Smart Structures and Integrated Systems 2014, SPIE, SPIE, Vol. 9057, (2014), pp. 882–888.
T. D. Truong, V. Q. Nguyen, B. T. Diep, D. H. Q. Le, D. T. Le, and Q. H. Nguyen. Speed control of rotary shaft at different loading torque using MR clutch. In A. Erturk, editor, Active and Passive Smart Structures and Integrated Systems XIII, SPIE, (2019).
EPS Division. Rotary seal design guide. Parker Hannifin Corporation, Catalog EPS 5350, (2006).
Q. H. Nguyen, N. D. Nguyen, and S. B. Choi. Design and evaluation of a novel magnetorheological brake with coils placed on the side housings. Smart Materials and Structures, 24, (2015).
C. A. C. Coello. Evolutionary multi-objective optimization: a historical view of the field. IEEE Computational Intelligence Magazine, 1, (2006), pp. 28–36.
K. Deb, A. Pratap, S. Agarwal, and T. Meyarivan. A fast and elitist multiobjective genetic algorithm: NSGA-II. IEEE Transactions on Evolutionary Computation, 6, (2002), pp. 182–197.
V. Ho-Huu, D. Duong-Gia, T. Vo-Duy, T. Le-Duc, and T. Nguyen-Thoi. An efficient combination of multi-objective evolutionary optimization and reliability analysis for reliability-based design optimization of truss structures. Expert Systems with Applications, 102, (2018), pp. 262–272.
T. Le-Duc, V. Ho-Huu, and H. Nguyen-Quoc. Multi-objective optimal design of magnetorheological brakes for motorcycling application considering thermal effect in working process. Smart Materials and Structures, 27, (2018).
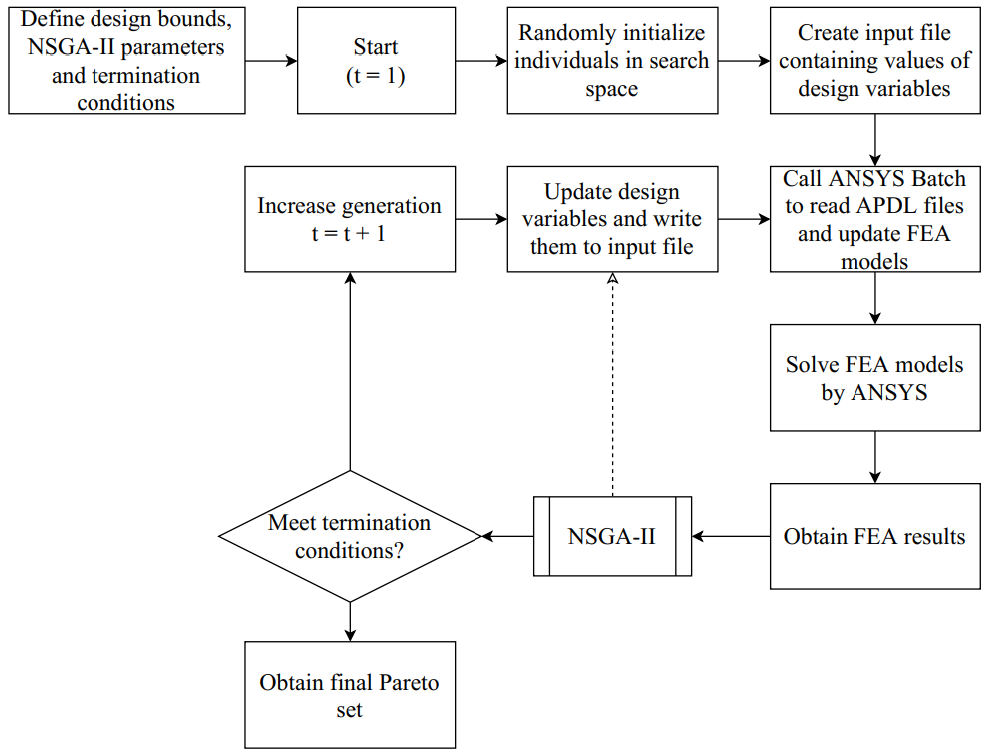
Downloads
Published
How to Cite
License

This work is licensed under a Creative Commons Attribution-ShareAlike 4.0 International License.